Engineering Firm Shows How The BMW i3 Is Revolutionary
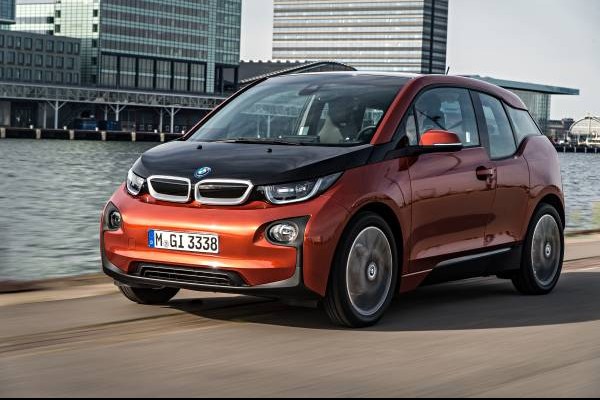
The BMW i3 might look weird and isn’t a vehicle that gets everyone’s blood pumping, but it’s what’s under the skin that counts the most. As Green Car Reports pointed out recently, engineering firm Munro & Associates uploaded to YouTube a teardown video of the electric car, and the results are compelling.
» Related: 2016 BMW 3 Series Gets a Light Refresh and More Power
The firm says that the i3 is paving the way for a revolution in how cars are manufactured, not only by BMW but across the entire industry. The car’s structure is made of carbon fiber, making it the first of its kind in any high-volume application. That fact allowed BMW to do things that aren’t possible with a steel or aluminum structure. It’s created using a mold, with holes cut using water jets instead of drills or other tools. Suspension and engine bushings are incorporated into the frame, which means some traditional parts aren’t even necessary, helping cut down on weight and bulk.
Other revelations include the fact that BMW glues the body panels to the i3′s frame. It presents an advantage since BMW could alter the car’s look without having the change the structure. Munro & Associates also found that the vehicle is outfitted with hooks in the front that are attached to the front suspension. During a collision to the front corner, like in the IIHS’ small overlap test, the wheel is turned away from the car so it isn’t pushed into the footwell where it could cause serious leg or foot injuries.
Plenty of people are concerned about battery life with electric cars. It seems BMW designed the i3′s battery so that individual cells and be replaced, helping the battery last longer and keep maintenance costs down.
Green Car Reports notes that A Sandy Munro, who is the CEO of Munro & Associates, has praised the i3 before. He claims that the innovative manufacturing methods BMW uses likely means the i3 actually generates a profit, unlike other electric cars on the market today.